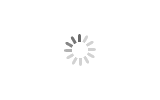
Agricultural Vehicle Brake Lining 300X90
Brand FEIROEN
Product origin ZAOYANG
Delivery time 30 DAYS
* low noise and dustproof
* silent brake action.
* less fading and heat resistant up to 400° C
* sharp and safe braking performance.
* excellent friction performance and stopping power, Allow for sensitive braking
BRAKE LININGS 300*90 / 300*60/ 400*80
Dimension (inner arc length×width×thickness): 300*90 / 300*60/ 400*80
Application: All kinds of Agricultural vehicles
Early friction plate
Motor vehicles must have transmission and braking in use, which requires the use of friction plates. The early friction plates were made of cotton, cotton, leather, etc. as a base material, and were processed into brake lining or brake bands. The disadvantage is that the heat resistance is poor. When the friction surface temperature exceeds 120 ° C, cotton and cotton will gradually coke and even burn. As the speed and load of the vehicle increase, the braking temperature increases accordingly, and such friction materials are no longer sufficient for use. So the new friction material - asbestos friction material was born.
Asbestos staple fibers and fabrics and fabrics can be used as the substrate for the friction material. Because of its lower price, it quickly replaced cotton and cotton as the main base material in friction materials. In 1905, the asbestos brake band was applied, and the friction properties and service life, heat resistance and mechanical strength of the products were greatly improved. Beginning in 1918, a combination of asbestos staple fibers and asphalt was used to make molded brake lining. In the early 1920s, phenolic resin began to be industrialized. Because its heat resistance was significantly higher than that of rubber, it quickly replaced rubber and became the main binder material in friction materials. Since phenolic resins are relatively inexpensive compared to other various heat-resistant synthetic resins, asbestos-phenolic friction materials have been widely used in various countries since then.
Current car brake lining
At present, our common brake pad formulations mainly include semi-metal formula, less metal formula, NAO formula, ceramic formula and so on. There are many parameters for automotive brake lining, such as friction coefficient, shear strength, thermal decay resistance, etc., which are required to meet national standards. If you use a brake pad of poor quality, you may not be able to stop the car, the braking distance is too long, etc., which may cause traffic accidents. However, if the friction coefficient of the brake pad is too large, it is easy to cause the tire to lock when the car brakes, resulting in loss of control of the burning piece or the vehicle, which jeopardizes the safety of the driver.
Brake pad wear
For the car, we all know that the brake system of the car is extremely important for the safety of the car. In the brake system of a car, the braking force is mainly generated by the friction of the brake pad and the brake disc. Therefore, the brake pad is an important part of the brake system, and it is the protector of cars and people.
First of all, the material and structure of the inferior brake disc or brake drum can easily cause abnormal wear of the brake lining. Secondly, the brake calipers of the brake system are damaged for a long period of time, causing the brakes to not return, so that long-term dragging of the sheets and the discs (drums) can also cause abnormal wear. Finally, the materials used for the brake lining are not satisfactory and the design density of the brake pad friction layer is unreasonable, which may also cause abnormal wear of the brake lining. Here to remind everyone, whether it is the brake lining on the disc brakes or the brake lining on the drum brakes, the brake lining on the brakes should be replaced in time to avoid the safety hazard.