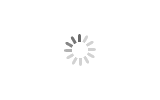
Barke Pads 29331
Brand FEIROEN
Product origin CHINA
Delivery time 35 days
Supply capacity As your request
1. High quality assurance with EMARK certification.
2. OE quality braking compliant, bringing added safety and reliability.
3. Excellent stopping power
4. Extended pad and rotor life
5. Low noise
6. Consistent braking effort and pedal feel.
7. Wire mesh & adhesive layer provide secure attachment to backing plate.
8. Steel backing plate with corrosion resistant coating.
9. Installation hardware include in every kit.
10. Visual wear slot indicates when brake pads need to be replace.
Automotive disc brake pads inspection
Brake torque detection
The principle of the brake of the disc brake pad is to generate friction between the friction pairs by applying a braking force to form a braking torque opposite to the direction of rotation of the brake disc, thereby causing the brake disc to decelerate and stop. It can be seen that braking force or braking torque is one of the key factors affecting braking performance. Most of the methods for detecting the braking force are to use a sensor to collect signals and then transmit them to the host computer for analysis.
Gate gap detection
The gate clearance refers to the gap between the brake pad and the brake disc when the brake pad is in the release state, and its size has a great influence on the braking performance such as the safety and efficiency of the brake system. A common method for detecting the gate gap is to establish a detection system consisting of a sensor, a signal acquisition module, a signal processing module, a computer, and related software.
Brake temperature detection
The disc brake process is an energy conversion process. The kinetic energy of the mechanical system is converted into frictional heat. Some of the heat is dissipated into the air, and most of the rest of the heat is absorbed by the brake pads, which causes the temperature of the brake friction pair. Raise. The increase in temperature causes the physical and chemical properties of the friction material to change, resulting in thermal degradation of the braking performance. The detection method of braking temperature is divided into direct method and indirect method.
Brake vibration and noise detection
Vibration and noise caused by friction during manufacturing are also one of the factors that reflect the instability of braking performance, and vibration and noise can seriously affect the driving safety, comfort and environmental protection of traffic vehicles. The vibration signal analysis and processing methods caused by friction mainly include: time domain method, frequency domain method and time-frequency method.
Why are some brake pads wearable and others need to be replaced frequently?
The wear resistance of the friction material reflects its service life and is one of the important indicators for measuring the performance of the friction material. Wear is unavoidable during normal use of the vehicle, especially the brake pads in the brake system. If the remaining thickness is less than 3-4mm, it must be replaced. People always want brake pads to have high wear resistance, low wear rate, and the longer the service life, the better.
Friction temperature is an important factor affecting the amount of wear. When the friction temperature reaches the thermal decomposition temperature of the polymer material, decomposition, carbonization and weight loss occur. As the friction temperature increases, these phenomena become more pronounced, and the amount of wear increases sharply, showing significant thermal wear. The use of suitable anti-wear filler and polymer adhesive with good heat resistance can effectively reduce the thermal wear of the friction material and prolong its service life. There are many ways to express the wear resistance of friction materials. Taking the wear index specified in the national standard "Brakes for Automobiles" as an example, the wear rate of the test material samples at a temperature of 100-350 ° C per block (50 ° C for one gear) on a fixed speed friction tester. The wear rate is the amount of volume wear when the unit is subjected to the unit friction work during the relative sliding process of the sample and the dual surface, and can be calculated by measuring the sliding distance of the frictional force and the thickness of the sample due to the reduction of the wear. Because the sample to be tested is affected by high temperature, it will produce different degrees of thermal expansion. Therefore, during the test of friction performance, the measured results may mask the thickness of the sample and even cause negative values, which cannot truly and correctly reflect the actual wear. At this time, in addition to measuring the volume wear of the sample, the mass wear result of the sample is additionally measured.