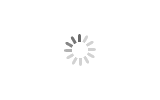
Diesel Engine Crankshaft
Brand BBL
Product origin China
The crankshaft is the main rotating part of the engine. After the connecting rod is installed, the up and down (reciprocating) movement of the connecting rod can be changed into a cyclic (rotating) motion. It is an important part of the engine. Its material is made of carbon structural steel or ductile iron. It has two important parts: the main journal and the connecting rod neck.
Crankshaft process analysis
When grinding the quenched steel crankshaft thrust surface, the following three types of burns may occur:
Tempering burn
If the temperature in the grinding zone does not exceed the phase transition temperature of the hardened steel, but exceeds the transformation temperature of the martensite, the tempered martensite structure of the surface metal of the thrust surface will be converted into a tempered structure with a lower hardness (Soch Body or tortoise), this burn is called temper burn.
Quenching burn
In addition to the quenching effect of the cooling liquid, the surface metal is quenched twice, so that the surface metal has a secondary quenched martensite structure, and its hardness is higher than that of the original tempered martensite. In its lower layer, due to slow cooling, A tempered structure (sordonite or stellite) having a lower hardness than the original tempered martensite appears, and this burn is called quenching burn.
Annealed burn
If the temperature in the grinding zone exceeds the phase transition temperature and no coolant enters in the grinding zone, the surface metal will produce an annealed structure and the surface hardness will drop sharply. This burn is called an annealed burn. In the crankshaft forming grinding, it is mostly such a burn.
Common damage to the crankshaft
Common forms of damage to the crankshaft are: journal wear, bending and torsion, and cracks.
(1) Wear of the journal. The wear of the crankshaft main journal and the connecting rod journal is uneven, and the wear parts have a certain regularity.
(2) The bending and torsion deformation of the crankshaft. The so-called crankshaft bending means that the coaxiality error of the main journal is greater than 0.05 mm. If the link journal angular error is greater than 0 degrees and 30 minutes, it is called crankshaft distortion.
(3) The fracture of the crankshaft. Cracks in the crankshaft occur mostly at the transition fillets between the crank and the journal and at the oil holes.
Overhaul of the crankshaft
The inspection of the crankshaft mainly includes crack inspection, deformation inspection and wear inspection.
(1) Inspection of cracks. After cleaning the crankshaft, first check for cracks. Crack testing can be performed with a magnetic flaw detector or dye penetrant. If the crankshaft detects cracks, it should generally be scrapped and replaced.
(2) Inspection and repair of crankshaft bending. The bending deformation shall be checked against the common axis of the main journals at both ends, and the radial runout error of the intermediate main journal shall be checked. During the test, place the spindle necks at both ends of the crankshaft on the V-shaped block of the inspection plate, and place the dial gauge contacts perpendicularly on the intermediate spindle neck, slowly turning the crankshaft one turn, the maximum indicated by the dial indicator The swing, that is, the radial runout error value of the intermediate main journal, if greater than 0.15 mm, should be pressure corrected. Below this limit, it can be corrected in combination with the grinding spindle. The correction of the bending deformation of the crankshaft can generally be performed by a cold pressure correction method or a tap correction method.
(3) Inspection and repair of crankshaft distortion. The test of the distortion of the crankshaft is to turn the connecting rod journal to the horizontal position, and use the dial gauge to determine the height difference between the two journals in the same orientation. This height difference is the amount of distortion. If the crankshaft is slightly distorted, it can be corrected directly on the crankshaft grinding machine in combination with the grinding of the connecting rod journal. The correction of the crankshaft distortion can be corrected by the hydraulic wrench torsion correction method.
(4) Inspection and repair of crankshaft journal wear. For the crankshaft that is allowed to be repaired by the flaw detection, the amount of journal wear must be checked: first check the journal for wear and damage, and then measure the roundness error and cylindricity error of the main journal and the connecting rod journal. The wear of the short journal of the crankshaft is mainly tested for roundness error, and for the long journal, the roundness and cylindricity error must be checked.
BBL forged crankshaft is applied on high power and RPM engines.
Comparing with casting crankshaft, our forged crankshaft provides more strength, finer grain size, improved microstructure and better fatigue resistance.
Both forging and machining lines are well equipped with most advanced facilities to meet different needs from various customers.
The production lines are equipped with 2 sets of 8000 ton double disk friction presses, 4 sets of 1600 ton high power screw presses, 2 sets of roll-forging machines, 6 sets of KUKA robots, 2 heat treatment lines for quenching and tempering, 1 test line for fluorescent magnetic particle flaw detection, 1 paint line, 3 machining lines.
Each production line is equipped with 3 KUKA robots and one mechanic arm to ensure quality consistency. The hitting power of 8000 ton double disk friction press can reach 12,000 ton, we are able to manufacture all kinds of forgings.
Both numerical control equipment and KBK are used to ensure processing precision and high efficiency.
Trunnion shaft is a cylindrical protrusion used as a pivoting point for dual axles to keep each wheel running properly on the bumpy road. BBL forging trunnion provides high strength to meet the harsh working environment requirement.
Our balance shaft specifications can be customized to be equipped on different trucks.