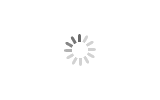
Gasoline Engine Crankshaft
Brand BBL
Product origin China
The crankshaft is the most important component in the engine. It takes the force from the connecting rod and converts it into torque through the crankshaft output and drives other accessories on the engine. The crankshaft is subjected to a centrifugal force of a rotating mass, a cyclically varying gas inertial force, and a reciprocating inertial force to cause the crankshaft to undergo a bending torsional load.
The role of the crankshaft:
It cooperates with the connecting rod to change the gas pressure acting on the piston into the rotating power, which is transmitted to the transmission mechanism of the chassis. At the same time, the valve train and other auxiliary devices, such as fans, pumps, generators, etc., are driven. During operation, the crankshaft is subjected to the action of gas pressure, inertial force and moment of inertia, which is subjected to large force and complicated force, and is subjected to the impact of alternating load. At the same time, the crankshaft is a high-speed rotating part. Therefore, the crankshaft is required to have sufficient rigidity and strength, has a good ability to withstand impact loads, and is resistant to wear and lubrication.
There are two types of support for the crankshaft.
One is a fully supported crankshaft and the other is a non-fully supported crankshaft.
Full support crankshaft:
The number of spindles of the crankshaft is one more than the number of cylinders, that is, one spindle neck is provided on each side of the journal journal. For example, a six-cylinder engine fully supports the crankshaft with seven main journals. The four-cylinder engine has five main journals for the full crankshaft. With this support, the strength and rigidity of the crankshaft are better, and the main bearing load is reduced and wear is reduced. Diesel engines and most gasoline engines use this form.
Non-fully supported crankshaft:
The number of spindles of the crankshaft is less than the number of cylinders or equal to the number of cylinders. This type of support is called a non-fully supported crankshaft. Although the main bearing of this support has a large load, the total length of the crankshaft is shortened, and the overall length of the engine is reduced. Some gasoline engines can adopt this type of crankshaft with a small load.
Processing Technology
Crankshaft roughing will use CNC lathes, CNC internal milling machines, CNC broaching machines and other advanced equipment to perform CNC turning, internal milling and car-broaching on the main journal and connecting rod journals to effectively reduce the deformation of crankshaft machining. Crankshaft finishing will extensively use a CNC-controlled crankshaft grinder to finish the journal. The grinding machine will be equipped with the automatic dynamic balancing device of the grinding wheel, automatic tracking device of the center frame, automatic measurement, automatic compensation device, automatic dressing of the grinding wheel, constant line speed and other functional requirements to ensure the stability of the grinding quality. High-precision equipment relies on the status quo of imports and is not expected to change in the short term.
BBL forged crankshaft is applied on high power and RPM engines.
Comparing with casting crankshaft, our forged crankshaft provides more strength, finer grain size, improved microstructure and better fatigue resistance.
Both forging and machining lines are well equipped with most advanced facilities to meet different needs from various customers.
The production lines are equipped with 2 sets of 8000 ton double disk friction presses, 4 sets of 1600 ton high power screw presses, 2 sets of roll-forging machines, 6 sets of KUKA robots, 2 heat treatment lines for quenching and tempering, 1 test line for fluorescent magnetic particle flaw detection, 1 paint line, 3 machining lines.
Each production line is equipped with 3 KUKA robots and one mechanic arm to ensure quality consistency. The hitting power of 8000 ton double disk friction press can reach 12,000 ton, we are able to manufacture all kinds of forgings.
Both numerical control equipment and KBK are used to ensure processing precision and high efficiency.
Trunnion shaft is a cylindrical protrusion used as a pivoting point for dual axles to keep each wheel running properly on the bumpy road. BBL forging trunnion provides high strength to meet the harsh working environment requirement.
Our balance shaft specifications can be customized to be equipped on different trucks.